Custom Porous Materials Reign
- François-Xavier Coudert, Physical Chemist
- 20 févr. 2018
- 10 min de lecture
Metal-organic frameworks (MOF) are new porous materials formed by assembling metal elements and organic, carbon-based bricks. This architecture makes them easy to synthesize and the number of potential structures is almost unlimited. Commercial applications, such as gas storage, are arriving on the market.
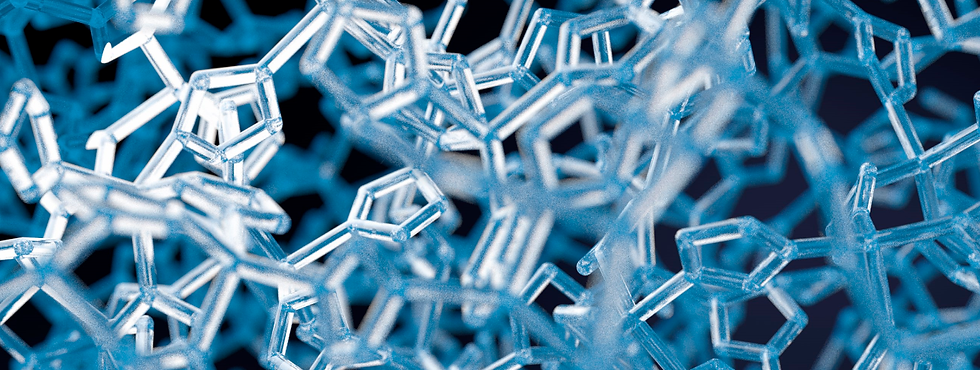
Photo © Ella Maruschenko
Cat litter, phosphate-free detergent, pumice stone, activated charcoal, etc. Porous materials are all around us in our daily lives. They contain empty spaces (or “pores”) of nanometric dimensions (1 nanometre = 10-9 metres) and have especially interesting properties precisely because of these pores.
When the size of these cavities reaches the nanometric scale, close to the diameter of molecules, the properties of porous materials become quite extraordinary. Firstly, because the smaller the pores, the larger the internal surface, and hence the “capacity” of the material: it can contain far more molecules. The contact surface between the solid and the molecules adsorbed in the pores, also called the interface, is then very large. Secondly, as the space accessible to these molecules is also limited, they behave very differently than would a “free” flowing fluid without the presence of the material. Both these effects (interface and confinement) give rise to specific properties of the materials. From a fundamental viewpoint, understanding the combination of these effects on the gases or liquids adsorbed raises many unanswered questions.
Nanoporous materials are present in our daily lives, but also in industrial applications. “Traditional” materials, widely sold today, are based on architectures which are either fully organic or inorganic. The first, including activated carbons, are produced using carbon-based materials - agricultural waste for example. The second may be natural minerals or synthetic aluminosilicates (*): this is the case for zeoliths, porous crystals widely used to refine crude oil, in petrochemicals, to soften water or to purify medical gases such as oxygen or nitrous oxide. Outside these two traditional families of nanoporous materials, is a new generation that breaks with these codes entirely. They combine organic and inorganic materials, mixed on a microscopic scale to form a new type of material with a potentially unlimited number of structures: metal-organic frameworks or MOFs for short.
MOFs were discovered at the start of the 2000s, highlighted and popularised by the team headed by the US chemist Omar Yaghi, then at Michigan University and now at Berkeley in California. These materials are formed by assembling of two types of elementary brick. The first are inorganic bricks, containing a metal ion, such as iron, zinc, cobalt, etc. The second are organic bricks, i.e. tiny carbon-based molecules. They are known as “organic ligands” as they possess chemical groups that can bond to the metal ions and form metal-ligand coordination bonds.
The assembled organic and inorganic bricks form a three-dimensional network called a “coordination polymer”; this is a hybrid organic-inorganic crystalline material, with alternating compounds on the molecular level. When the size of the connecting ligands is sufficiently large, empty space remains when the network is assembled and a nanoporous material is thus obtained. The formation of pores can also be promoted (compared to another, denser material structure) by the presence of structuring agents which occupy the pores during synthesis, to be evacuated before the material is used.
READY-TO-WEAR
What is one of the main advantages of MOFs over traditional porous materials ? The versatility of the elementary bricks. In this game of “molecular Lego”, the bricks of matter can be replaced according to the crystalline structure sought; this is “tailor-made” synthesis, whereas inorganic nanoporous materials are limited by their chemical composition and structure - like ready-to-wear. A MOF’s pores can be made larger or smaller by selecting longer or shorter organic ligands, while at the same time maintaining the same metal-ligand coordination method and hence the same structure. This means for example that a specific material can be created to separate gaseous mixtures, like a molecular sieve with hole size chosen according to the molecules to separate. It also means that molecular architectures can be built with porosities that smash all known records. In 2010, a material was manufactured that had 6,240 m2 of internal surface area... in a single gram of crystal!
The design of new materials does not stop there. By adding additional chemical groups to the organic ligand to cover the surface of the nanopores, the synthesized material takes on a special function. For instance, by inserting amine functions (NH2 chemical group), known for their strong bonds with CO2, a material can be built with a strong affinity for capturing and storing carbon dioxide. Or by using light-sensitive chemical groups, a material can be created that releases the stored molecules on command, by exposing it to light.
OVER 60 METALS USED
All the know-how of molecular chemistry is available to synthesize MOFs that incorporate complex organic bricks. But we can also “play” with the nature of the metal cations present, meaning that the geometry and the chemical properties of the material synthesized can be influenced, for example changing its chemical, mechanical or thermal stability. Over 60 metals have already been used in MOFs, and others are being studied. Like in all research, the discovery and exploration of this new family of materials has not been without surprises. Indeed, chemists’ fascination for these complex, supramolecular assemblies has led to quite a race to obtain the most porous structures possible, or that can store the most methane, hydrogen, etc.
In less than twenty years, more than 15,000 structures have been created. We only know the physical properties in detail of a few dozen of them; those on which a systematic study was conducted, because they are highly original or highly “effective” properties are suspected for a concrete application. By studying them, we realise that MOFs, built on intermolecular interactions that are weaker than the metal-oxygen bonds in inorganic materials, are sometimes capricious and show behaviour that was previously thought to be extremely rare or even impossible. In particular, these materials are extremely flexible and react easily to external physical or chemical stimulation: changes in temperature, pressure, exposure to light, to electrical or magnetic fields, etc. When the changes in structure caused by stimulation give rise to other properties (a change in optical properties for example), we use the term “smart materials”. This coupling can be exploited for practical applications: piezo-electric, thermo-electric or shape-memory materials. We know of materials that capture CO2 in their “normal” state, only to release it when exposed to light stimulation.
One rare behaviour of inorganic materials, revealed as common in MOFs, is negative thermal dilation. When a “traditional” solid is heated, it dilates and the volume it occupies grows larger. Caused by thermal agitation of the atoms within the material, this dilation plays a key role in solid mechanics. In practice it can be harmful, creating internal constraints in road bridges (mechanical forces between the bridges components, offset by including joints), or in dental compounds. In most MOFs, atomic movement caused by temperature is very different. This is due to their scaffold-type architecture. When the temperature increases inside a MOF, vibrations of the ligands (scaffolding bars) outside their axis brings the metal centres closer together instead of spreading them apart. Most MOFs therefore undergo contraction - a negative expansion coefficient!
They can be used in mechanical applications, such as engines or nanometric actuators. They can also be combined with a more traditional material, with a positive thermal expansion, to form a composite structure with zero thermal expansion. This is a potential alternative to the only technology that exists in this sector: Zerodur ©. This glass ceramic used in optics to make gigantic telescope mirrors, in microlithography or metrology (to make standards that are not temperature dependent) is very expensive. It is also impossible to vary its properties. Another example of MOF curiosities: the so-called “breathing” movements of some extremely flexible MOFs. Initially discovered by the team of Gérard Férey in Versailles and Susumu Kitagawa in Kyoto, these breathing solids change volume (between 50 and 300%) when dipped in a solvent (water, methanol, etc.) or when exposed to a gas (methane, carbon dioxide, etc.). Only some gels and polymers can achieve such performances, and this is the first time this behaviour has been seen in crystalline solids. In 2016, a German team at Dresden Technical University, designed a new type of flexible MOF based on copper ions: DUT-49. This smart material also has a completely counterintuitive response. In a “normal” material, when the pressure is increased, the quantity of gas adsorbed and the size of the materials pores are both increased. The extreme flexibility of DUT-49 revealed a surprise: after filling with gas up to a certain pressure (of the order of 0.1 to 0.3 atmospheres), it suddenly contracts and its volume reduces by half if the pressure continues to rise. This “abnormal” property, not allowed by the laws of thermodynamics, is only possible because the solid is in fact in a metastable state - like supermelted water which in some cases remains liquid even when slowly cooled below 0°C, its freezing point. MOFs therefore, have numerous potential applications, in particular in fields that deal with significant social issues (energy, environment, health), but also in niche processes. Like for most nanoporous materials, the separation, capture and storage of gases are their most natural applications.
The first fully commercial application of a MOF is the product TruPick by the start-up MOF Technologies (created around the work of Stuart James, a chemist at Queen's University Belfast). It was launched on the market in 2016 to limit ripening of fruit after harvesting. It comes in the form of a bag of gel, with the MOF inside, to be placed in the container among the fruit. It works on the storage and release of 1-methylcyclopropene, a molecule that inhibits the ethylene responsible for ripening.
In another field, since September 2016, the start-up NuMat Technologies, created in 2012 by scientists at Northwestern University in Illinois, United States, has been selling a system of cylinders, called ION-X, for the storage of hazardous or toxic gases. By using the absorption capacities of a blend of several MOFs, these bottles can store industrial gases such as phosphine, arsine and boron trifluoride (used in the electronics industry) at reduced pressures, thus limiting the risk of leaks of these highly toxic gases.
INDUSTRIAL SCALE
Both applications required not only the development and characterisation of porous structures, initially in the laboratory, but also a change of scale to enable the constraints of industrial-scale production to be overcome. Methods of synthesis, known in the laboratory at gram level, had to be adapted to reach quantities greater than a kilogram. Energy and environmental efficiency of the synthesis are key at these scales. Innovative processes are proposed, such as mechanosynthesis, used to produce materials directly by crushing and extruding reagents, using without the need for solvents. Numerous start-ups, created by scientists and often backed by universities, have been created over the last few years offering synthesis solutions and MOFs, and it is likely that the costs will fall and the number of products on the market will increase. In France, the CNRS plays a leading role and jointly owns 26 families of patents concerning MOFs.
Of the applications currently sought but still a long way from market, are those in the field of health and the environment. Results at the laboratory or prototype stage, hold great hope for this new family of materials. Time will tell whether the industrial scale is possible and whether these fascinating materials will find a place in our homes and cars.
(*) An aluminosilicate is a mineral in the silicate group in which some silicon atoms have been replaced with aluminium atoms.
POROUS PROPERTIES...IN A LIQUID

Ordinarily, metal-organic frameworks (better known by their acronym “MOF”) are solid, porous materials. The team of François-Xavier Coudert (Chemistry ParisTech/CNRS) and Thomas Bennett (Cambridge University, United Kingdom) have just developed one of the very first porous materials... that is a liquid. And that is not all: it retains its porous properties when converted to a solid (vitreous). This MOF is comprised of a network of pyramid structures; each one is comprised of a zinc atom surrounded by four organic molecules (imidazolates), and it is this assembly which gives it its name - ZIF-4. To demonstrate the behaviour of their materials, the chemists brought it to a fusion temperature of 865 kelvin (about 592°C) in an argon tube oven and allowed it to cool to room temperature. They also used a variety of digital simulations to study how it reacted at even higher temperatures (the maximum was 2250 kelvin, or nearly 1977°C). By combining two methods of diffraction (neutron and x-ray), and molecular simulations, they verified conservation of its remarkable porosity when passing from one phase to the other. More than just a laboratory curiosity, porous liquids (very few in existence) can find applications in the catalysis and separation of liquid phases, as well as being used to form new vitreous materials.
Photo : ZIF-4 has a crystalline and porous appearance at room temperature (top). At high temperature (bottom), it is liquid and remains porous.
THE MAGICIAN OF CRYSTALLOGRAPHY
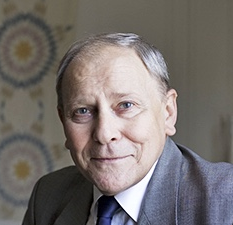
In 2004, Gérard Férey (1941-2017), one of the pioneers in porous solids, developed with his team the most porous material in the world; this material could contain 400 times its own volume in gaseous CO2: MIL-101 (material of the Institut Lavoisier, his laboratory in Versailles). He was awarded the CNRS Gold Medal in 2010.
HOPE FOR MEDICINE AND THE ENVIRONMENT
MOFs are raising considerable hope in the fields of the environment and medicine. Some specialists are even envisaging MOF drugs, encapsulating active therapeutic ingredients within their pores. The idea is to use a non-toxic porous material as a vector to modulate and control delivery of an active ingredient. According to the surface chemistry of MOF nanoparticles, work in the laboratory and on animals has shown that cancer cells can be specifically targeted, increasing the effectiveness of treatment while reducing the side effects. In the environmental sector, the team of Omar Yaghi of Berkeley University in California, has developed a prototype to capture water from the air in desert conditions, by adsorbtion within the pores of a MOF and condensation. This device operates using the strong bonds formed between the MOF and water, to capture it in extremely dry environments (up to 20% humidity) at night. During the day, heat and sunlight provide the energy to extract the water from the material which will be condensed.
TO KNOW MORE
• An explanatory video of what are the MOFs, by one of the pioneers of the field, Omar Yaghi.
• The CNRS valorisation website, Fist SA; it lists all technology-free technology offers related to MOFs and managed by the CNRS and Fist SA.
• The website of the porous solids excellence network.
> AUTHOR
François-Xavier Coudert
Physical Chemist
François-Xavier Coudert is a physical chemist, specialising in porous materials and the behaviour of gases and liquids at their interfaces. He is a researcher at the CNRS, in the Paris Chemistry Research Institute. He did a PhD at Paris-Sud University, and a post-doctoral degree at London University College.
Comments